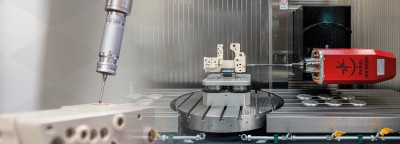
A new technique: Milling an additive manufacturing product
Within BKB Precision, we are constantly innovating and improving the manufacturing process and participating in challenging, innovative projects of our clients. One of our most recent projects is a great example of this. In collaboration with the client and suppliers, we took on a new challenge of machining a 3D-printed PEEK product, with several challenges to overcome.
5-Axis milling of additive manufacturing products
About 2.5 years ago, we were approached by a customer asking if we could also manufacture a certain titanium product from PEEK (Polyetheretherketone), which initially seemed like an impossible task.
Such a development process often involves many challenges, where we have to push our limits and learn new skills. At BKB Precision, for example, we were faced for the first time with the task of post-processing a product produced by additive manufacturing using a 5-axis milling machine to meet very precise specifications.
Moreover, during this development process we also learned how to place inserts with a very high frequency (20,000 hertz) in a product, which contributes to better adhesion and can be essential due to thin wall thicknesses.
We have since worked with the customer to make this job a success and now produce several of these products every year.
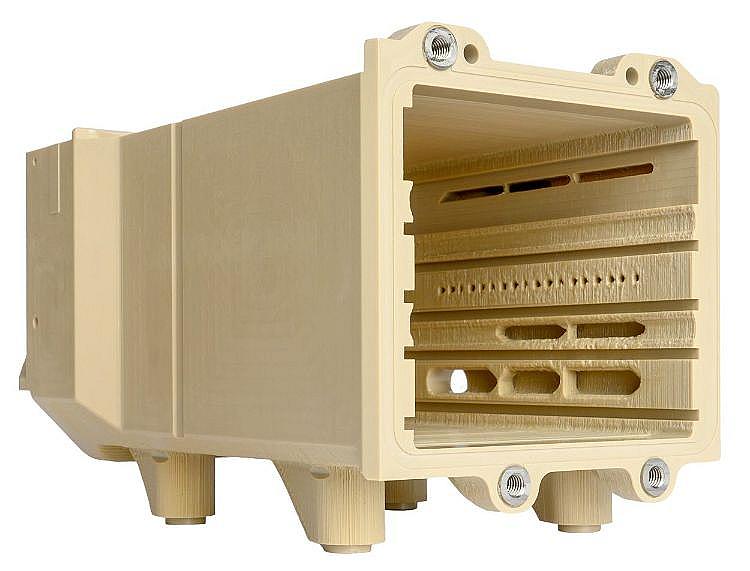
The challenge of new technology
One challenge when turning or milling a 3D-printed product is that not all products have exactly the same dimensions. This leads to tight tolerances, especially when some parts are a millimeter or even a tenth of a millimeter longer or shorter. Normally we would then mill off that millimeter, but in this case that is not possible because it would make the interfaces too thin.
Nevertheless, at BKB Precision we managed to find a method to accurately post-machine 3D printed products so that they meet the specifications provided by the customer.
Unique collaboration
Within BKB Precision, we take short lines of communication, transparency, openness and honesty for granted, a culture that also suits the participants within this project. This collaborative culture ensures good communication, preventing obstacles and keeping development cycles short.
Because the product is already in use several times, more opportunities for improvement are still revealing themselves. The search for achieving the optimum of this product translates into changes in the specifications. BKB Precision makes every effort within the project to adopt those changes and translate them into the right machining strategies. With the ultimate goal of delivering a unique and relevant part for the right application.
Wondering how we can help you with your project?
Contact one of our specialists now and we will gladly take up the challenge with you!